L'azienda Balfor srl ci segnala il progetto QBX. Di seguito pubblichiamo il loro depliant tecnico informativo su questo interessante progetto.
Il progetto QBX nasce dall'idea di produrre un combustibile naturale che sia prodotto in forma e dimensioni standardizzate, che costi poco, che sia derivato dal legno.
Video su come vengono prodotti i cubetti di legno
Progettazione
La forma a cubetto è stata presa da subito in considerazione come risposta alla già esistente forma a cilindro (pellet) ma che secondo noi poteva dare dei vantaggi interessanti.
Il cubo, con le sue 6 facce e 8 spigoli, offriva secondo noi una buona capacità di innesco (maggiore è la superficie offerta all'aria e maggiore è la facilità di innesco del fuoco, in più, gli spigoli essendo la parte "sottile del cubo" si accendono per primi e più facilmente rispetto al resto, portando poi la combustione verso il centro del cubetto) e una buona capacità di creare intercapedini tra un cubo e l'altro per il passaggio dell'aria che serve per rendere ottimale la combustione.
Provammo pertanto a creare dei piccoli cubi in legno di acacia di 5 cm per 5 cm in maniera del tutto manuale, li essiccammo al sole e provammo a bruciarli in un braciere ad aria forzata auto costruito. Il risultato visivo era soddisfacente, si presentava una fiamma molto calda e una combustione molto regolare del prodotto a fronte di uno scarto incombusto molto più basso della normale legna da ardere. Sembrava, secondo queste nostre prove, che la resa di combustione della legna ridotta in cubi fosse significativamente maggiore rispetto alla normale legna da ardere la quale presenta una percentuale maggiore di incombusto (dipende dal grado di essiccazione e dall'essenza del legno).
Questa nostra percezione era dovuta al fatto che se dopo la combustione la cenere è poca, vuol dire che quasi tutto il combustibile si è trasformato in calore e questo era sicuramente un vantaggio importante per il nostro raffronto legna / cubetto. Anche il fumo prodotto a combustione in corso sembrava essere minore rispetto al legno.
Ragionando sulle dimensioni del singolo cubo, si presentarono da subito ai nostri occhi dei campi di applicazioni interessanti per caldaie a carico automatico, ma soprattutto per le già esistenti stufe a pellet, il carico automatico di una stufa o di una caldaia è infatti possibile solo con un combustibile regolare. E' impossibile il carico automatico di una stufa o caldaia a legna proprio a causa di questa irregolarità di forma del combustibile.
Si presentò infatti la possibilità di utilizzare la legna da ardere con tutti i suoi vantaggi (facile reperibilità, naturalezza del prodotto, tracciabilità, alto rendimento) con i vantaggi delle stufe e caldaie non a legna (carico automatico, programmazione delle accensioni, scarsa necessità di effettuare pulizia degli impianti ecc ecc).
Riuscendo a creare un cubetto di adeguate dimensioni ed adeguato grado di umidità si sarebbero potute utilizzare le caldaie a pellet con un combustibile più naturale che poteva avere una tracciabilità facile e soprattutto creato sul posto con legname locale.
Procedemmo a creare i cubetti di 1 cm di lato sempre in modo manuale e a provare a bruciarlo nella stufa a pellet.
Qui nacquero le prime difficoltà.
Il cubetto non era abbastanza essiccato e la stufa si accendeva a fatica, in più il cubetto era un po' più grande del pellet e si incastrava (anche a causa della sua forma spigolosa) nelle pareti della coclea alimentatrice bloccandola e facendo spegnere la stufa.
Continuammo con molteplici prove di dimensionamento incentrate sulla riduzione delle dimensioni dei nostri cubi arrivando ad un prodotto che misurava 1cm x 1cm x 7mm che non si incastra più nella coclea ma che necessita di essere essiccato un po' meglio rispetto a quelli delle prove precedenti.
Molteplici prove sono state fatte con le essenze legnose più disparate non evidenziando una significativa disparità tra le varie tipologie vegetali.
Scartammo solo i resinosi per paura che, con l'eventuale colo di resina, più cubi potessero incollarsi causando ulteriori blocchi nella stufa.
Essiccandolo per circa una settimana con essiccazione naturale (semplice esposizione ai raggi solari) il prodotto bruciava bene senza spegnersi.
Visto che il nostro cubo funzionava abbiamo potuto cominciare lo studio ed in seguito la realizzazione della macchina per produrlo.
Pensammo dapprima di procedere con una incisione della faccia rotonda del tronco a griglia utilizzando dei dischi abrasivi montati su un albero che ruotasse ad alta rotazione. Così facendo si sarebbero creati i cubi affettando questa griglia incisa. Nelle prove che facemmo si creava del fumo e della polvere quindi abbandonammo da subito l'idea che comunque non ci aveva convinti del tutto sin dall'inizio.
Procedemmo con lo sviluppo di un altro metodo che sembrava più efficace e più facilmente realizzabile, cioè quello di dividere il processo in due parti: la creazione di fette di legno del giusto spessore e poi la lavorazione di queste fette con un elemento che "grattasse via" delle porzioni a forma di cubetti.
Dopo diverse bozze di disegno, abbandonammo anche quest'altra idea perché "grattando via" i cubetti dalla fetta, i cubetti erano delle specie di riccioli inutilizzabili per il nostro scopo.
Un'altra ipotesi che prendemmo in seria considerazione fu la semplice estrusione della fetta in tanti piccoli cubetti tramite una griglia affilata. Questo sistema che subito si rivelava semplice, mostrò difficoltà sempre crescenti fino a rivelarsi irrealizzabile.
Infatti una griglia sulla quale si spinge con forza una sottile fetta di legno si sfondava. Aumentando gli spessori della griglia per aumentarne la resistenza, si aumentava anche la forza che il legno faceva per entrare in tale griglia e si arrivava ad un ennesimo sfondamento. Qualora il problema sfondamento fosse stato superato (aumentando gli spessori e la forza fino a superare la forza di coesione del legno) si presentava l'impossibilità di far uscire i singoli cubetti che si incastravano nella griglia con una tale pressione da non poter più uscire.
Pensammo alla fine di procedere con dei rulli che ruotavano adiacenti e che potessero incidere le nostre fette in modo da poter creare questi cubi, però, questo metodo ci obbligava a fare un passo indietro e a tornare alle fette di legno.
Queste fette, infatti, per entrare in questi rulli ed uscirne incise dovevano avere uno spessore precisissimo, approssimato al decimo di millimetro.
Questa precisione è inusuale per delle macchine taglio legna ma era una prerogativa necessaria per poter procedere. Senza questa precisione i rulli non avrebbero potuto funzionare perché lo spessore delle fette, se superava anche di pochissimo la distanza tra i due rulli, avrebbe causato il blocco di tutto il meccanismo.
Accantonato temporaneamente il sistema dei rulli e ci concentrammo sulla affettatrice che, se prima poteva essere realizzata sfruttando delle tecnologie già in nostro possesso, ora doveva essere del tutto rivista.
Procedemmo con la realizzazione della affettatrice che tagliava con una lama di sega a nastro (a scarto bassissimo e contenuto bisogno energetico pochi KW consumati rispetto alle altra lame).
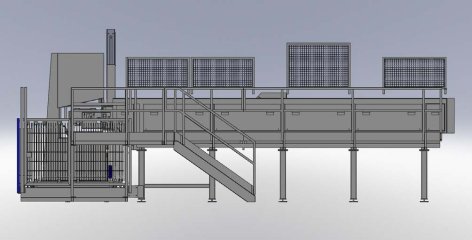
La struttura venne fatta portante per accogliere ogni tipo di legname e soprattutto in quantità elevata.
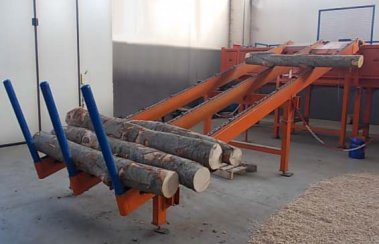
L'idea infatti era quella di avere una macchina che potesse andare avanti da sola e quindi doveva poter caricare quanto più legname possibile e soprattutto più lungo possibile.
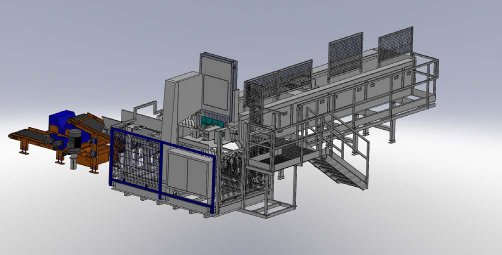
L'affettatrice è stata costruita per poter lavorare non-stop, quindi con componenti sia meccanici che elettrici che idraulici di primaria qualità e circuiti sovradimensionati per evitare surriscaldamenti e alterazioni di funzionamento. I componenti sensibili a polvere e sporco sono stati tutti nascosti integrandoli nella parte bassa della macchina per evitare i tempi morti risultanti dal fermo macchina.
E' stato anche creato un sistema di aria forzata per la pulizia eventuale dell'apparato, in tal modo si può soffiare via la segatura qualora questa crei dei problemi ai sensori.
La struttura e stata fatta elevata in modo da poter si proteggere sotto di essa le parti potenzialmente delicate, ma anche per poter agevolare lo spostamento delle fette. (dall'alto al basso e non viceversa).
Il carico dei tronchi avviene quindi su un caricatore a catene che porta i tronchi in una vasca di taglio la quale, grazie ad una speciale forma del fondo e tramite degli speciali ritentori, permette di portare il tronco o i tronchi in fase di affettatura senza che questi si muovano lateralmente. Uno spintore spinge i tronchi con un avanzamento pari allo spessore delle fette.
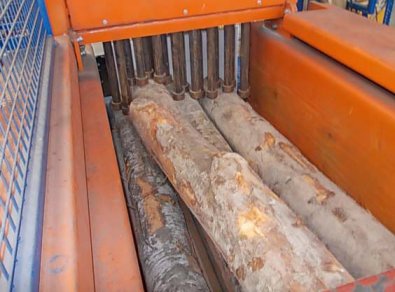
Per l'affettatura e stato scelto il metodo della lama a nastro perché grazie al suo spessore ridotto crea uno scarto bassissimo (effettuando cosi tanti tagli si rischiava di avere una quantità di scarto pari al 50% del prodotto se si fossero utilizzati altri metodi, e soprattutto la segatura non sarebbe stata facilmente utilizzabile ma sarebbe stata un prodotto da considerarsi di materiale di risulta).
L'affettatrice è stata inoltre concepita con un tappeto trasportatore solidale al taglio che evita che le fette una volta tagliate possano rotolare in direzioni impreviste.
Le fette grazie a questo sistema procedono tutte nella stessa direzione in modo ordinato senza accavallamenti delle une sulle altre.
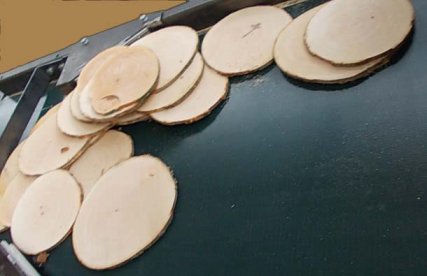
Grazie a questo sistema abbiamo così abbandonato l'idea di un vaglio a "cappello cinese" che raccogliesse le fette e le convogliasse verso la seconda fase. Tale "cappello cinese" infatti risultava di complessa realizzazione e soprattutto di funzionalità non certa perché, anche se poteva essere funzionale nell'evacuare le fette tagliate, non evitava del tutto il rischio di accavallamento. Abbiamo ottenuto un risultato soddisfacente ottimizzando le velocità del tappeto trasportatore e modellando lateralmente le paratie dello stesso operando un disegno che permettesse alle fette di rotolare sul nastro e poi di "coricarsi" sul tappeto prima di procedere.
La prima versione del modulo di taglio aveva un controllo del taglio e delle varie movimentazioni necessarie tutto di tipo HARDWARE che permetteva una precisione troppo limitata del taglio e nonostante tutte le regolazioni effettuate e gli sforzi atti ad incrementarne la precisione necessitò di essere totalmente rifatto perché le fette non risultavano mai dello spessore desiderato. Si procedette alla realizzazione del nuovo controllo del modulo taglio che permetteva una precisione decisamente maggiore. Il nuovo modulo taglio venne equipaggiato di PLC con regolazioni proporzionali di velocità e la fetta in teoria aveva uno spessore precisissimo.
In pratica però si verificava una situazione diversa.
Lo spessore continuava a non essere regolare e preciso.
Indagando a fondo capimmo che questa anomalia era causata dal fatto che lo spintore, imprimendo una spinta al legno, permetteva che questo scivolasse minimamente (impercettibile quasi alla vista) sul fondo della vasca, sballando di fatto l'effettivo avanzamento e di conseguenza lo spessore delle nostre fette. Questo scivolamento non era né quantificabile e né contenibile perché dipendeva dal peso del legno caricato in vasca. Più peso c'era e più la precisione si avvicinava a quella desiderata, meno peso c'era caricato in vasca (vasca carica solo a metà della sua capacità) e meno le fette erano precise.
Lo stesso problema si verificava con l'alleggerimento della vasca dovuto all'avanzamento dei tagli. Se i primi tagli (vasca pesante) erano precisi, gli ultimi non lo erano perché la vasca si alleggeriva a mano a mano che il tronco si accorciava.
Si presentò quindi la necessita di produrre un arresto meccanico con l'integrazione di sensori magnetici di avanzamento tronchi e dopo innumerevoli prove e regolazioni finalmente iniziò a dare i risultati che tutti ci aspettavamo.
Ad ogni modifica ed implementazione verniciammo il modulo taglio, tale decisione venne intrapresa per ottenere un prodotto finito migliore e più presentabile ma si rivelò essere una decisione sbagliata in quanto ad ogni modifica bisognava sverniciare la parte da modificare (per poter effettuare la saldatura) dopo la saldatura la vernice che si era scaldata ingialliva, e doveva essere rimossa nuovamente per poi procedere ad una ulteriore riverniciatura. Abbandonammo pertanto (limitatamente al modulo di incisione) l'idea di verniciare di volta in volta.
La produzione dei cubetti
Avendo finalmente le fette del giusto spessore potevamo procedere alla produzione del secondo modulo, quello della riduzione delle fette in cubetti.
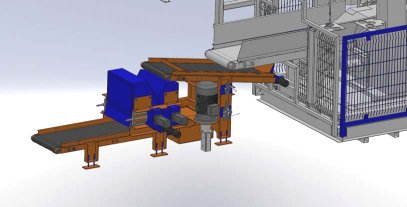
Avendo individuato la strada per noi migliore da seguire abbandonando gli altri due sistemi precedentemente citati (grattare via dalle fette con uno speciale utensile disegnato appositamente allo scopo oppure estrudere dalle fette esercitando forte pressione contro una speciale griglia) potevamo procedere con i primi disegni di tali rulli.
Da subito si presentarono molti problemi. Primo fra tutti il disegno dei due rulli che dovevano incastrarsi l'uno nell'altro per poter oltre ad incidere anche dividere i cubetti in modo che si staccassero l'uno dall'altro. L'incastro doveva prevedere anche lo spazio per il cubetto che veniva inciso e che doveva rimanere tra i rulli senza incastrarsi troppo a fondo altrimenti non sarebbe più uscito.
Per far si che questo fosse realizzabile bisognava prevedere un rullo composto da tante lame affilate affiancate e uno con tanti dentini affiancati. Tra dentini e lame doveva esserci un incastro perfetto.
Le lame, se erano troppo affilate, si danneggiavano piegandosi facilmente, se erano troppo spesse, non permettevano che il cubetto si staccasse dal rullo. La stessa cosa valeva per il rullo composto da tanti dentini.
Altri quesiti si posero al momento di trasmettere il moto ai rulli e provammo ad ipotizzare alcune casistiche e decidemmo per motorizzare i rulli con dei motori idraulici con trasmissione a catena.
Dopo aver fatto il primo prototipo che, dopo essere stato più volte rivisto, si rivelò funzionante, procedemmo alla realizzazione di quello che avrebbe dovuto essere l'originale, quindi identico al primo prototipo ma solo più grande; e all'ennesima prova, notammo che il rischio che i cubetti si incastrassero persisteva nonostante avessimo ridisegnato più volte i rulli per fare in modo da scongiurare questo rischio.
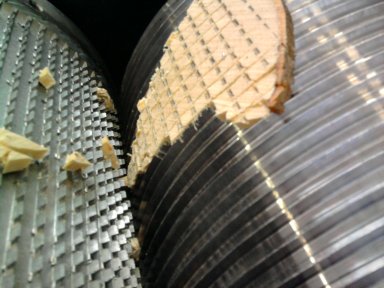
Provammo con la tecnica delle spazzole con le quali facemmo una rudimentale prova che si rivelò non funzionale e difficilmente realizzabile.
Prevedemmo quindi un set di "pettini" di pulizia per i rulli che dovevano scorrere nelle profondità tra lame del rullo incisore longitudinale e i denti del rullo incisore trasversale (quello con i dentini) evacuando i cubetti che si incastravano.
Il primo set di pettini non lavorava in modo ottimale ed effettuammo un altro prototipo per arrivare alla soluzione che abbiamo considerato migliore ma non abbastanza robusto.
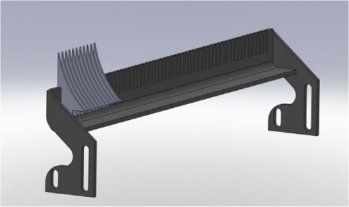
Questi pettini funzionavano bene sul rullo incisore longitudinale ma risultavano inefficaci per il rullo incisore trasversale. Per poter far si che i rulli facessero il loro lavoro dovemmo aumentare la velocità con conseguente danneggiamento dei pettini. Ne consegui un ulteriore prototipo che rimase definitivo sul rullo longitudinale.
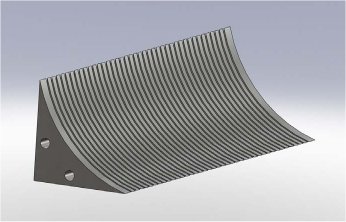
Rimase il problema dei cubi incastrati sul rullo incisore trasversale. Ci fu quindi il bisogno di realizzare un altro dispositivo che sostituisse il pettine del rullo con i dentini trasversali.
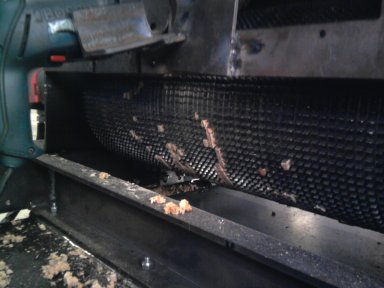
La conseguenza fu una terza riprogettazione dei rulli e un conseguente terzo realizzo degli stessi. Procedemmo quindi con un disegno dei rulli diverso molto più complesso ma che sembrava essere decisamente migliorato rispetto alle altre due versioni.
Questi rulli presentavano delle aste o camme che dovevano muoversi verso l'esterno dopo la fase di incisione.
Il movimento e stato studiato lavorando sul principio dei cerchi eccentrici che girano l'uno nell'altro.
Le astine,o camme collegate al cerchio interno dovevano allargarsi solo in un punto cioè il punto subito successivo all'incisione del cubetto, né prima e né dopo e fu quello che realizzammo.
Quindi i rulli si presentavano con delle profondità maggiori per accogliere queste astine e quindi procedemmo alla realizzazione degli stessi in materiale più duro.
Per effettuare tale lavorazione nella gola del rullo abbiamo dovuto realizzare un utensile ad oc che avesse la forma del negativo della gola stessa.
Se infatti i cubetti non fossero stati espulsi alla prossima incisione un altro cubetto si sarebbe accavallato bloccando il meccanismo.
Alla prova conseguente la realizzazione dei rulli valutammo il risultato come molto soddisfacente.
Rimasero da sostituire i motori idraulici che risultavano veloci abbastanza ma non adeguatamente potenti. Dopo svariate prove individuammo i giusti motori idraulici e li tarammo con pressione molto elevata (300 bar) e rapporto di velocità 1:2.5
Alla prova pratica notammo subito che con questo nuovo metodo la casistica di inceppamento era scesa notevolmente e anche l'usura dei componenti si rivelò ridotta.
Procedendo nell'accoppiamento dei due moduli con un semplice nastro trasportatore, ci accorgemmo che era necessario garantire al prototipo le necessarie precauzioni atte all'utilizzo in sicurezza quindi effettuarono dei ripari con dei sensori e delle chiusure inaccessibili in prossimità di tutte le zone sensibili al pericolo e vennero chiuse con dei carter quelle parti che non dovevano venire neanche accidentalmente a contatto con l'utilizzatore.
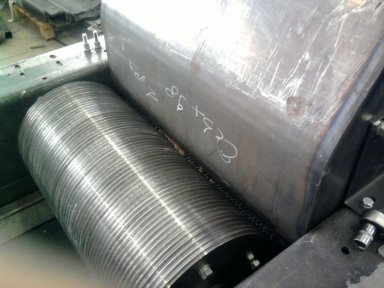
A prototipo finito , procedendo con le prove. Riscontrammo dei risultati soddisfacenti ma annotammo alcune migliorie fattibili e che in parte già abbiamo cominciato a sviluppare.
La segatura, oltre ad essere ridotta alla minore quantità possibile, poteva essere recuperata ed eventualmente pressata e mischiata al prodotto finito arrivando quindi al traguardo auspicato dello scarto ZERO. Ad oggi abbiamo provveduto a recuperarla con dei sistemi di aspirazione e abbiamo individuato alcuni metodi già presenti sul mercato per poterla comprimere in pellet.
L'essiccazione che secondo il nostro progetto avviene solo naturalmente, potrebbe essere effettuata anche in maniera forzata riscaldando il legno già ridotto in cubi con delle lampade radianti (il legno sminuzzato in cubetti si asciuga molto velocemente). Oppure altro metodo sarebbe quello di sostituire il tappeto di evacuazione dei cubetti con un tappeto a cingoli in ferro e scaldarlo dall'interno sempre con delle lampade, cosi facendo i cubetti si muoverebbero per alcuni secondi su un supporto caldo e ne uscirebbero sufficientemente essiccati.
Potremmo anche eventualmente aumentare la velocità di taglio utilizzando una affettatrice a più lame, ma questo sistema che aumenterebbe in teoria la produzione, si rivela essere di realizzazione difficile anche se non impossibile.
Prove di combustione
Ad oggi abbiamo fatto più prove di combustione con i cubetti.
Le prime prove di combustione in stufa a pellet si sono rivelate fallimentari per il fatto che i cubetti in alcuni rari casi si presentavano aggregati e andavano a bloccare la coclea.
L'ultima prova effettuata utilizzando i cubetti risultanti dall'ultima versione di rulli è stata molto soddisfacente perché la stufa a pellet riusciva ad accendersi con i soli cubetti e in più, continuando ad alimentarla, sviluppava calore tanto quanto il pellet, consumava meno prodotto e rilasciava meno cenere del pellet.
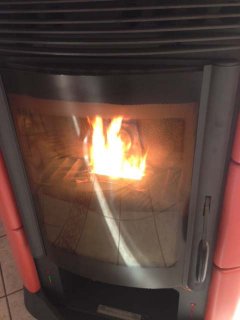
Tanto che lo stesso proprietario della stufa si è detto contento della prova e ha manifestato la sua disponibilità ad utilizzare il QBX in futuro.
Imballaggio
Rimangono da decidere i metodi di imballaggio del prodotto finito.
Sono state prese in considerazione due tipologie di imballaggio, quella in cartone riciclato oppure il nylon (imballaggio analogo al pellet).
La dimensione ottimale è quella di 8KG che in volume equivale circa ai 15KG di pellet.
Provando ad imballare il prodotto appena tagliato e non essiccato questo presentava la comparsa di muffe di colore bianco.
Provando invece ad insacchettare il prodotto essiccato naturalmente per 7 giorni a basse temperatura e all'ombra (con il solo contatto dell'aria quindi), le muffe non si sono presentate e le caratteristiche del prodotto si sono manifestate costanti anche dopo un periodo di insacchettatura, la combustione in questo caso era soddisfacente.
Altri esperimenti verranno effettuati con una essicazione minore per valutare quale possa essere il periodo minimo.
In fine l'imballaggio in cartone, (funzionando bene il nylon) è stato per ora scartato in quanto il cartone potrebbe assorbire facilmente umidità e mettere a repentaglio la conservazione del prodotto.
Per maggiori informazioni contattare Daniele Forestello e Gianluca Ballario, al numero 0175 289391, presso www.balfor.it, azienda impegnata a realizzare i ferri del mestiere, per i professionisti del legno, cioè macchine dedicate ad un uso intensivo e sottoposte ad ogni tipo di stress derivato da utilizzo estremo.